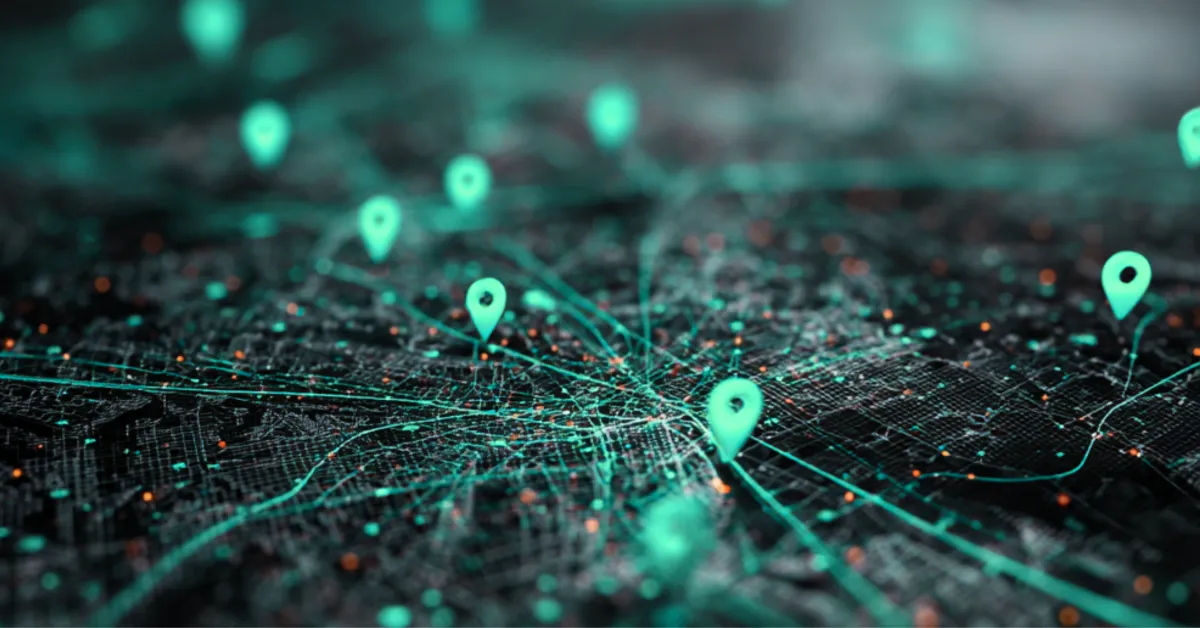
Industrial IoT and Location Intelligence: Transforming Manufacturing Through Mapping Data Services
Executive Summary
The convergence of Industrial Internet of Things (IoT) and location intelligence is revolutionising manufacturing operations, creating unprecedented opportunities for operational efficiency and competitive advantage. As Industry 4.0 technologies mature, mapping data services have emerged as critical enablers for smart factory transformation, predictive maintenance, and supply chain optimisation. With global industrial automation spending projected to exceed $350 billion by 2030, manufacturers are increasingly leveraging geospatial intelligence to optimise production processes, enhance asset tracking, and improve decision-making capabilities.
The Industrial IoT Revolution and Spatial Intelligence
Defining Industrial Location Intelligence
Location intelligence represents the strategic use of geospatial data to identify and solve complex business problems within industrial environments. In manufacturing contexts, this technology combines GPS tracking, sensor networks, and advanced analytics to provide real-time visibility into production assets, workforce movements, and operational processes. Unlike traditional manufacturing systems that operate in isolation, location intelligence creates interconnected networks that enable data-driven decision making across the entire production ecosystem.
The integration of IoT devices with geospatial technologies has created what industry experts term "spatial manufacturing intelligence" - a comprehensive approach to understanding how physical space, time, and operational data interact within industrial facilities. This convergence enables manufacturers to optimise everything from equipment placement and workflow design to predictive maintenance scheduling and energy consumption patterns.
Key Technologies Driving Industrial Spatial Intelligence
Sensor Networks and Real-Time Data Collection: Modern industrial facilities deploy extensive sensor networks that capture location-specific data including temperature, vibration, pressure, and equipment status. These sensors work in conjunction with GPS and indoor positioning systems to create detailed spatial maps of operational conditions. Advanced LiDAR mapping sensors, such as the Slamtec Mapper M2M2, can achieve mapping accuracy of less than 0.02 meters across areas up to 100,000 square meters, enabling precise asset tracking and facility optimisation.
Edge Computing and Distributed Processing: The implementation of edge computing architecture allows for real-time processing of geospatial data at the point of collection, reducing latency and enabling immediate responses to operational changes. This distributed approach is particularly valuable for time-sensitive applications such as predictive maintenance alerts and safety monitoring systems, where millisecond response times can prevent equipment failures or safety incidents.
Machine Learning and Spatial Analytics: Advanced machine learning algorithms specifically designed for spatial data analysis enable manufacturers to identify patterns and correlations that would be impossible to detect through traditional methods. These systems can predict equipment failures based on spatial patterns of wear, optimise maintenance schedules based on geographic clustering of assets, and improve overall equipment effectiveness through location-based analytics.
Asset Tracking and Management Revolution
Digital Asset Visibility
Traditional asset management systems often struggle with real-time visibility and accurate location tracking. Modern mapping data services transform this challenge by providing comprehensive digital asset visibility through integrated tracking solutions. These systems enable manufacturers to view asset information in real-time on geographical maps, streamlining operations and improving decision-making capabilities.
Visual mapping systems allow operators to scan through all assets simultaneously, viewing detailed information about each item including asset codes, names, addresses, and visual documentation. This capability dramatically reduces the time required for asset audits and enables more proactive maintenance strategies.
Predictive Maintenance Through Spatial Intelligence
Predictive maintenance represents one of the most valuable applications of industrial mapping data services. By combining location data with equipment sensor information, manufacturers can identify spatial patterns that indicate potential equipment failures. This approach moves beyond traditional time-based maintenance schedules to provide condition-based maintenance recommendations that optimise equipment performance while minimising downtime.
The integration of spatial intelligence with predictive maintenance systems enables manufacturers to map maintenance requirements across their facilities, optimising technician routes and resource allocation. This spatial approach to maintenance planning can reduce maintenance costs by up to 20% while improving equipment reliability.
Supply Chain and Logistics Optimisation
Geospatial Analytics in Supply Chain Management
The application of geospatial analytics in supply chain management has transformed how manufacturers approach logistics optimisation. By analysing spatial relationships between suppliers, manufacturing facilities, and distribution centres, companies can optimise delivery routes, reduce transportation costs, and improve overall supply chain resilience.
Real-time tracking capabilities enable manufacturers to monitor goods movement throughout the supply chain, providing visibility into potential bottlenecks and delays. This enhanced visibility allows for proactive decision-making and helps minimise the impact of supply chain disruptions.
Risk Management and Contingency Planning
Geospatial analytics provides manufacturers with powerful tools for identifying and mitigating supply chain risks. By analysing geographic data, companies can identify potential risks such as natural disasters, political instability, and transportation bottlenecks that could impact their operations. This spatial approach to risk management enables more robust contingency planning and improved supply chain resilience.
Industry 4.0 and Smart Factory Implementation
Levels of Smart Factory Development
The evolution toward smart factories follows a structured progression through four distinct levels. Level 1 focuses on data collection from sensors and production equipment, creating the foundation for spatial intelligence. Level 2 involves connecting this data to centralised systems, providing a single source of truth for operational decisions. Level 3 introduces advanced analytics and automation, while Level 4 represents fully autonomous operations with minimal human intervention.
Mapping data services play crucial roles at each level, providing the spatial context necessary for effective data interpretation and decision-making. As manufacturers progress through these levels, the importance of location intelligence becomes increasingly apparent.
Manufacturing Automation Platform Integration
Modern manufacturing automation platforms integrate mapping data services to provide comprehensive operational visibility. These cloud-based systems enable manufacturers to design, automate, deploy, and operate manufacturing equipment through unified interfaces that incorporate spatial intelligence.
The integration of mapping data with automation platforms creates digital twins of manufacturing facilities, enabling virtual testing and optimisation before physical implementation. This approach reduces implementation risks and accelerates the deployment of automation solutions.
Workforce Optimisation and Safety Enhancement
Labor Analytics and Spatial Intelligence
Location intelligence provides manufacturers with powerful tools for workforce optimisation. By analysing employee movement patterns and work area utilisation, companies can identify opportunities to improve efficiency and reduce wasted time. This spatial approach to labor analytics enables more accurate forecasting of workforce requirements and better allocation of human resources.
Spatial analytics can reveal insights into employee productivity patterns, helping identify areas where additional training or process improvements may be beneficial. This data-driven approach to workforce management can significantly improve operational efficiency while reducing labor costs.
Safety and Compliance Monitoring
Industrial mapping data services enable comprehensive safety monitoring through spatial awareness systems that track employee locations and identify potential safety hazards. These systems can automatically alert supervisors when employees enter restricted areas or when safety equipment is not properly utilised.
The integration of location intelligence with safety management systems provides manufacturers with real-time visibility into workplace safety conditions, enabling proactive interventions that prevent accidents and ensure regulatory compliance.
Future Trends and Emerging Technologies
Digital Twin Integration
The convergence of digital twin technology with industrial mapping services represents a significant advancement in manufacturing intelligence. Digital twins create virtual replicas of physical manufacturing assets, enhanced with real-time data from sensors and location tracking systems. This integration enables manufacturers to simulate different operational scenarios and optimise performance before implementing changes in the physical environment.
Challenges and Implementation Considerations
Data Integration and Interoperability
One of the primary challenges in implementing industrial mapping data services is ensuring seamless integration with existing manufacturing systems. Manufacturers must carefully consider data formats, communication protocols, and system compatibility when implementing these solutions.
Security and Privacy Concerns
The collection and analysis of detailed location and operational data raise important security and privacy considerations. Manufacturers must implement robust cybersecurity measures to protect sensitive operational data while ensuring compliance with relevant regulations.
Conclusion
Industrial IoT and location intelligence are fundamentally transforming manufacturing operations through sophisticated mapping data services. As manufacturers continue to embrace Industry 4.0 technologies, the integration of spatial intelligence with production systems will become increasingly critical for maintaining competitive advantage.
The convergence of sensor networks, edge computing, and advanced analytics is creating unprecedented opportunities for operational optimisation, predictive maintenance, and supply chain enhancement. Manufacturers who successfully implement these technologies will be well-positioned to thrive in an increasingly competitive global marketplace.
The future of manufacturing lies in the intelligent integration of physical and digital systems, with mapping data services serving as the crucial bridge between spatial reality and operational optimisation. As these technologies continue to evolve, we can expect even greater innovations in how manufacturers leverage location intelligence to drive efficiency, safety, and profitability.